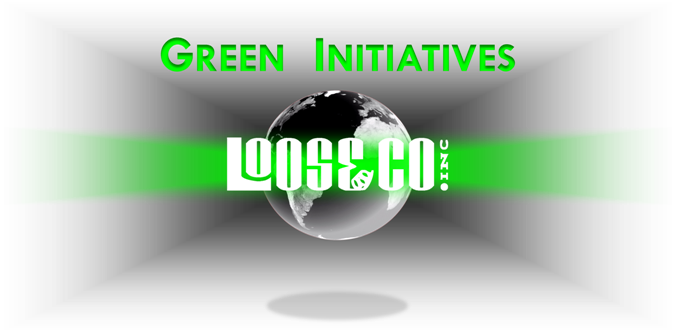
Loos & Co. è costruita su una fiera tradizione di innovazione in un settore apparentemente vecchio, quello della fabbricazione dell'acciaio. In più di cinquant'anni di esistenza siamo cresciuti da una start-up con due garage per auto a leader riconosciuto del settore. Risultati del genere si ottengono solo facendo le cose per bene. Questo atteggiamento di fare le cose per bene si estende al di là dei nostri processi produttivi, fino al modo in cui ci comportiamo come cittadini dell'azienda. Sebbene ultimamente si parli molto di conservazione dell'ambiente, noi ci preoccupiamo da tempo dell'impatto che abbiamo sull'ambiente e da anni pratichiamo la conservazione. Abbiamo pensato che potessero interessarvi alcune delle iniziative ecologiche che abbiamo avviato nel corso degli anni per ridurre la nostra impronta ambientale.
1) 1993 - Sostituzione di centinaia di luci, motori, cinghie e azionamenti con versioni ad alta efficienza energetica. Il risparmio elettrico stimato è stato di oltre 190.000 chilowattora all'anno.
2) 1999 - Deviazione del calore del refrigeratore da trenta tonnellate. Il calore di scarico di questo refrigeratore di processo è stato deviato nel reparto adiacente del Mulino a Corde per fornire il riscaldamento dell'area. Questo fornisce calore a circa 17.000 metri quadrati di spazio industriale. In quest'area non c'è un forno e quindi non viene bruciato petrolio per il riscaldamento localizzato.
3) 2000 - Il calore di scarto di un secondo refrigeratore da trenta tonnellate è stato deviato verso l'area di stagnatura per il riscaldamento. Il calore di scarico di questo refrigeratore di processo è stato deviato nel reparto adiacente per fornire il riscaldamento dell'area. Questo fornisce calore aggiuntivo a circa 6.000 metri quadrati di spazio industriale. In quest'area non c'è un forno e quindi non viene bruciato petrolio per il riscaldamento localizzato.
4) 2000 - Nelle aree degli uffici sono stati installati circa trenta sensori di movimento per controllare l'illuminazione dei singoli uffici, delle riunioni e delle aree comuni. Questi sensori si attivano automaticamente e le luci si spengono quando le aree non sono occupate. Il risparmio elettrico stimato è stato di 2080 kilowattora all'anno.
5) 2000 - Ricottura Recupero del calore dei forni. Sono state installate unità di trattamento dell'aria per catturare il calore emesso dai forni di ricottura. Due unità deviano il calore nelle aree di produzione adiacenti e due ricircolano e distribuiscono il calore ad altre aree dello stesso grande locale. In quest'area non ci sono forni a olio e quindi non viene bruciato olio per riscaldare circa 45.000 metri quadrati di spazio industriale.
6) 2001 - Porte ad alta velocità. Sono state installate porte automatiche ad alta velocità per isolare un'area climatizzata dello stabilimento. Rendendo l'operazione automatica e veloce, abbiamo risparmiato l'energia necessaria per raffreddare 7.000 metri quadrati di superficie.
7) 2001 - Controllo e riparazione delle perdite d'aria. È stata eseguita un'indagine completa sull'aria compressa per identificare e riparare le perdite. L'aria compressa è un componente essenziale per il funzionamento delle apparecchiature, ma è anche una forma di energia costosa. Il programma ha permesso di risparmiare oltre 200.000 chilowattora all'anno di energia elettrica che altrimenti sarebbe andata sprecata.
8) 2001 - Aggiornamento del sistema dell'aria compressa. Un importante aggiornamento del sistema ha aumentato l'efficienza dell'impianto di aria compressa, soprattutto per quanto riguarda lo stoccaggio e la distribuzione. Le linee principali, un anello di processo completo e un grande serbatoio di stoccaggio hanno contribuito a migliorare l'efficienza del sistema, con un risparmio di oltre 260.000 chilowattora all'anno di energia elettrica.
9) 2004 - Tutte le entrate degli uffici principali sono state aggiornate in modo da includere una delimitazione secondaria dalle intemperie (vestibolo o simili). Questo isolamento supplementare trattiene il calore in inverno e riduce il carico dell'aria condizionata in estate.
10) 2005 - Illuminazione della fabbrica - Fase I. Abbiamo sostituito 281 apparecchi di illuminazione con luci fluorescenti T-5 a basso consumo energetico. Inoltre, sono stati installati 26 sensori di movimento in modo che le luci si spegnessero automaticamente quando le aree non erano occupate. Questo programma ha permesso di risparmiare oltre 354.000 chilowattora all'anno di energia elettrica.
11) 2006 - Illuminazione dello stabilimento - Fase II. Abbiamo sostituito altri 280 apparecchi di illuminazione con luci ad alta efficienza energetica. Inoltre, sono stati installati altri 40 sensori di movimento in modo che le luci si spengano automaticamente quando le aree non sono occupate. Questo programma ha permesso di risparmiare circa 114.000 chilowattora all'anno di energia elettrica.
12) 2007 - Apparecchi a risparmio idrico. Sono stati installati impianti di risparmio idrico nei bagni di tutta la struttura. I nuovi rubinetti automatici e gli apparecchi a basso consumo d'acqua (o senza acqua) hanno contribuito a ridurre il nostro consumo d'acqua di circa 60.000 galloni all'anno.
13) 2007 - Forno per oli usati. È stato installato un forno speciale per bruciare oli usati e altri combustibili. Questa fornirà calore a un'ampia area di produzione. Utilizzando questo olio per il riscaldamento, abbiamo ridotto la quantità totale di gasolio da riscaldamento acquistato di 1.500 galloni durante la prima stagione di riscaldamento. Questo risparmio dovrebbe raddoppiare l'anno prossimo.
14) 2007 - Cataloghi stampati - La versione elettronica del nostro catalogo è stata resa disponibile online anziché solo in forma cartacea. Inoltre, il catalogo è disponibile su CD-ROM, riducendo ulteriormente il consumo di carta grazie alla riduzione dei materiali di stampa e spedizione.
15) 2007 - Sostituzione del motore e dell'azionamento ad alta efficienza da 125 CV. Un motore A/C ad alta efficienza ha sostituito un motore a corrente continua e un gruppo elettrogeno molto vecchi, con un risparmio di oltre 260.000 kilowattora all'anno di energia elettrica. Questo risparmio di energia elettrica sarebbe in grado di alimentare oltre 400 abitazioni medie all'anno!
16) 2010 - Loos & Co., Inc. ha installato un generatore da 2 megawatt per sostenere il programma di gestione del carico del Connecticut. Questo programma consente a Loos di generare la propria energia in caso di eventi di "load shed". Il programma, sponsorizzato da CT light and Power (CL&P), riduce la domanda di energia elettrica durante le ore di punta, di solito nei caldi mesi estivi.
17) Programmi di riciclaggio
a) tutte le lampadine
i) HPS
ii) Mercurio
iii) Fluorescente
b) Tutte le batterie a secco
i) alcalino
ii) Nichel-cadmio
iii) Nichel-metallo-idruro
c) Scarti di estrusione / plastica
d) Olio di trafilatura (processo)
e) Rottami metallici (di processo)
i) S/S
ii) Acciaio al carbonio
iii) Bronzo fosforoso e altri non ferrosi
iv) Alluminio
f) Cartone
g) I rifiuti generici vengono selezionati e bruciati, non interrati.